
|
Welding
We use a combination
of TIG (heli-arc), MIG (wire), and Resistance (spot) welding processes
to properly weld MGA's together.
MIG welders are the
most common welders in restoration shops today, and Eclectic Motorworks
is no exception. However, we do not use our MIG welders as our primary
machines. We use them primarily on frame restorations, as the welds
from a MIG welder most accurately simulate the factory welds.
For most sheet metal repairs, such as fender and body tub patches,
we use our TIG welder. We butt-weld panels into place and metal
finish the welds to the point where they are almost undetectable.
Since the TIG welding process is more precise and produces a more
malleable weld, we feel this is the best process for these types
of repairs.
Using our TIG welder, we can also repair the aluminum panels in
an MGA. We often repair door tops (where the side curtain mounting
hole are) as well as cracks in doors, bonnets, and boot lids. Commonly,
we will weld luggage rack mounting holes shut in boot lids when
owners choose not to put a luggage rack back onto their cars. |
When it comes time
to attach sills, pillars, or any of the other panels that were spot-welded
to the body from the factory, we use our state-of-the-art HTP spot
welder.
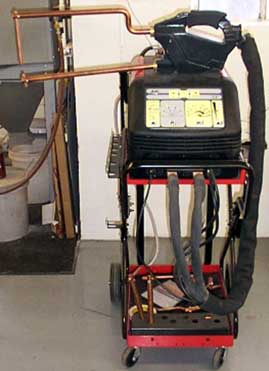
This micro-processor
controlled welder allows us to duplicate factory welds quickly.
Not only do these welds look and function exactly like factory welds,
they create far less distortion than typical rosette (plug) welding
process would cause. An added bonus is that these welds can be produced
more quickly and require less finishing time and abrasives--saving
money in the restoration.
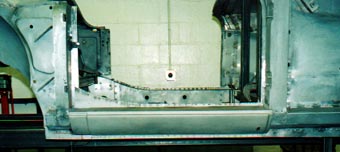
If you'd like to learn
more about our welding process, we can send you welding samples.
Please call or e-mail for more details.
|

|